In today’s rapidly evolving manufacturing landscape, computer numerical control (CNC) technology has emerged as a game-changer. With its ability to automate and optimize various manufacturing processes, CNC technology has revolutionized the industry by enhancing precision, efficiency, and productivity. In this blog, we will delve into the significant role CNC technology plays in modern manufacturing and explore its impact on the industry.
Enhanced Precision
CNC technology has significantly improved precision in manufacturing processes. By utilizing computer-aided design (CAD) software and advanced algorithms, CNC machines execute intricate operations with utmost accuracy. The ability to precisely control tool movements, cutting speeds, and positioning allows for the creation of complex and intricate components, leading to higher quality end products.
Increased Efficiency and Productivity:
Automation lies at the core of CNC technology, leading to increased efficiency and productivity. CNC machines operate continuously, reducing manual intervention and downtime. Once programmed, they can perform repetitive tasks with consistency, speed, and minimal error rates. This streamlined workflow translates into higher production rates, shorter lead times, and improved overall manufacturing efficiency.
Versatility and Flexibility
CNC technology offers remarkable versatility and flexibility in manufacturing. The same CNC machine can be programmed to produce a wide range of components, simply by altering the software instructions. This flexibility allows manufacturers to adapt quickly to changing market demands, reducing the need for specialized machinery and enabling cost-effective production of diverse products.
Complex Geometries and Customization
With CNC technology, the manufacturing industry can tackle complex geometries and intricate designs that were previously unattainable. CNC machines can precisely carve intricate shapes, holes, and contours, ensuring consistency across multiple components. Moreover, customization has become more accessible, as CNC machines can adapt to individual product specifications and easily switch between different production runs.
Improved Safety
CNC technology prioritizes operator safety. By minimizing the need for manual intervention, workers are exposed to fewer hazards associated with traditional manufacturing methods. The automated nature of CNC machines reduces the risk of accidents caused by human error, such as incorrect tooling or mishandling of materials. Manufacturers can focus on providing a safe working environment and additional training to ensure employees can maximize the benefits of CNC technology.
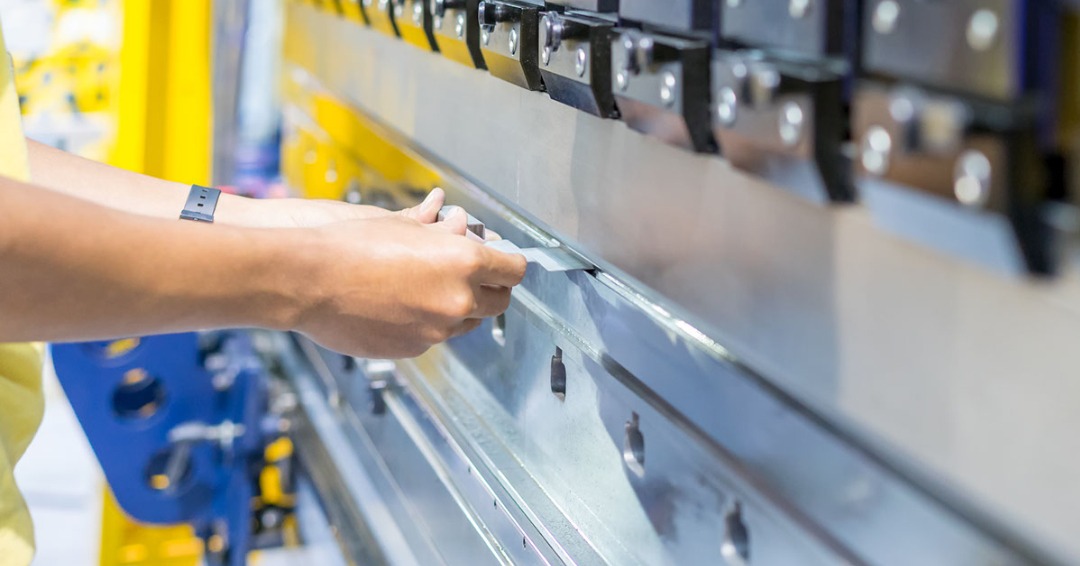
Data-Driven Decision Making
CNC technology generates a wealth of data during the manufacturing process. This data can be analyzed and used for continuous process improvement. Manufacturers can identify bottlenecks, optimize tooling, and fine-tune production parameters based on real-time data. The insights gained from data analysis contribute to informed decision-making, reducing waste, and improving overall manufacturing efficiency.
Integration with Industry 4.0
CNC technology seamlessly integrates with the principles of Industry 4.0, the fourth industrial revolution characterized by the fusion of automation, data exchange, and advanced manufacturing technologies. CNC machines can connect to the Industrial Internet of Things (IIoT), enabling real-time monitoring, predictive maintenance, and remote diagnostics. This connectivity and data exchange facilitate smart manufacturing, improving production agility and responsiveness.
Becoming CNC operator
Becoming a CNC operator in the UK involves several key steps. First, it’s important to acquire a high school diploma or equivalent qualification.
Additionally, pursuing further education in engineering, manufacturing, or a related field can provide a competitive advantage. Vocational courses, apprenticeships, or certifications specifically focused on CNC machining are also available and can enhance your knowledge and skills.
Gaining practical experience is crucial, so seek out entry-level positions or apprenticeships that offer on-the-job training. This hands-on experience allows you to apply your knowledge, develop skills, and become familiar with various CNC machines and processes.
Continual learning and staying updated with the latest advancements in CNC technology through workshops, seminars, and networking events are also important for professional growth. By following these steps and building a strong resume, you can position yourself as a qualified CNC operator in the UK job market.
Are you interested in becoming CNC operator? This role is expected to grow in the coming years and here at Industrial Work Solutions we already seen increased demand for qualified CNC operators from our clients. If you’re looking for a position, don’t hesitate to contact us at 01524 840 622 or info@industrialworksolutions.co.uk today!
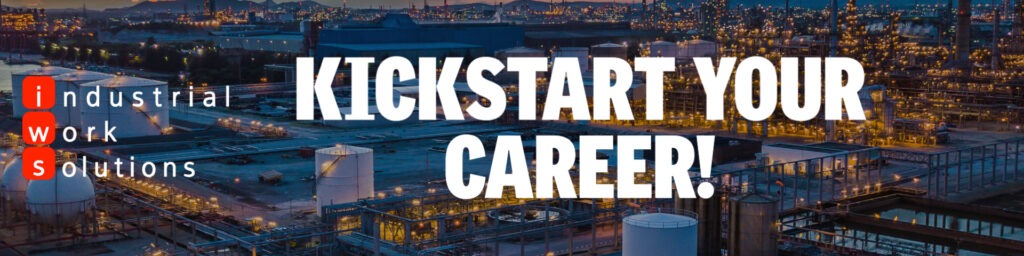
Recent Comments